When properly selected and applied, oil skimmers are highly economical solutions for separating oil from water to allow its reuse or safe disposal. However, there are certain applications that can expect optimal results. Typical applications best suited for oil skimmers encompass:
Wastewater Sumps
Wastewater sumps where removing floating hydrocarbons can reduce the cost of disposal and lower the contingent liabilities of wastewater discharge.
Most manufacturing or processing facilities have water systems where waste oil collects in a central tank or sump. Skimming the floating oils with little water content can reduce the cost of disposal and lower the contingent liabilities of wastewater discharge.
Coolant and Cutting Fluids
Coolants and cutting fluids where skimming tramp oils extends coolant life, improves the quality of machined parts, reduces irritating smoke that forms during machining, lessens the chance of dermatitis and helps prevent the fluid from developing a "rotten egg" odor.
Oil skimmers utilize the differing specific gravity between oil and coolant/water to remove tramp oils. A motor driven belt that is typically constructed of an oleophilic, or oil attractant material, is placed into a coolant sump or reservoir. As the belt moves through the coolant, it attracts tramp oils. The oil is scraped off by a wiper and deposited into a container.
Heat Treating
Heat treating operations where trench oils must be removed from heat-treated parts, and can be captured with a skimmer for re-use or disposal. This reduces oil purchases, prolongs wash water life and lowers disposal costs.
Parts Washers
Parts washers where removing floating oils from a wash tank prevents re-contamination of the parts as they are removed from the fluid and extends fluid life.
Industrial parts washers, paint lines, and machine shops all have a need to remove oil from water. Abanaki oil skimmers are trusted throughout the automotive industry to extend coolant life, reduce disposal costs, and avoid fines from municipal sewer districts.
Food Processing
Food processing facilities where the removal of vegetable oils, greases and animal fats from a plant's wastewater stream reduces processing and disposal costs.
Oil skimming is the most reliable and lowest cost method of removing food greases and oils from process wastewater. An oil skimmer uses the difference in specific gravity between oil and water, allowing the oil skimmer belt to attract frying oils, vegetable oils, greases, and animal fats as the belt passes through the surface of the water. The simple belt-and-motor approach is proven to operate unattended and reliably for decades with little maintenance.
Parking Lots, Garage and Service Facilities
Parking lots, garages and service facilities where waste oil from leaks, spills and other sources must be retrieved from sumps before water can be discharged to storm or sanitary sewers.
Outdoor Ponds, Lakes and Basins
Outdoor ponds, lakes and basins where floating oils are present, skimmers provide inexpensive and effective removal, solving a serious environmental problem.
Recovery/Monitoring Wells
Recovery/monitoring wells where a belt skimmer can be used instead of a down well pump to remove oil, fuel and other hydrocarbons. Generally, this is more cost-effective and reduces maintenance headaches. Skimmers can reach depths of 200 feet or more and remove floating products despite fluctuating water tables.
The PetroXtractor is a well oil skimmer that makes use of the differences in specific gravity and surface tension between oil and water. These physical characteristics allow the unit’s continuous belt to attract floating oil in the well. After picking up the oil, the belt travels over the head pulley on the drive unit and through tandem wiper blades. The oil is then scraped off both sides of the belt and discharged through a 1-1/4″ ID hose. The unique bearing-less design of the tail pulley (immersed in the well water) with its tethered frame allows it to perform three important functions: it keeps proper tension on the belt, prevents accidental loss down the well, and keeps the belt centered in the casing.
Remediation Processes
Remediation processes where skimmers can be used effectively in tandem with other means and reduce the overall cost and increase the speed of the cleanup. For example, when using bio-remediation techniques, skimmers can be used to first remove the bulk of the oil from the groundwater. Then more biological agents may be used to clean up the remaining contamination. The remaining oil will clean up faster, as there will be less of it.
Sometimes called pump-less groundwater remediation systems, oil skimming is the lowest cost way to remove hydrocarbon contamination from groundwater. Oil skimming alone may clean water to acceptable levels or be used as a pre-filter treatment. It is the most inexpensive way to remove LNAPLs or DNAPLs.
To learn more about oil skimmers, please contact our experts at 440-543-7400 or visit our website: www.abanaki.com
Oil Skimmers Get the Dirty Jobs Done
In the video, oil skimmer is shown removing spent lubricant from a collection tank in a steel production facility. Due to the extreme heat resulting from the steel making process, lubricant used for conveyor bearings often leaks into the cooling water, creating a floating goop that can foul filters further upstream.
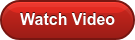